TYPES OF COMPRESSORS
Types Of Industrial Gas Compressors
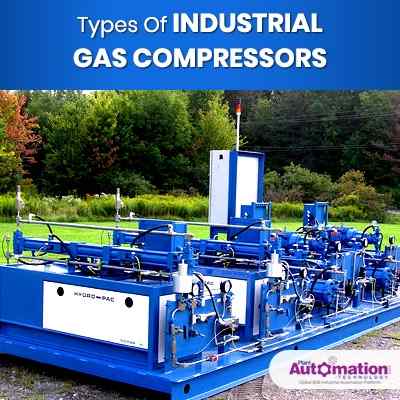
The gas compressors used in industries are mechanical devices that increase the pressure of a gas by reducing its volume. Unlike liquids, which are relatively incompressible, the gases are compressible and hence the compressor reduces the volume of a gas. The industrial gas compressors are used to increase the static pressure of the gas and distribute it at a specified flow rate and pressure in a process application. In process industries, compressors are prime movers of gas and air. The compressors are similar to pumps, as both increases, the pressure on a fluid and both can transport the fluid through a pipe. The compression of gas naturally increases its temperature and the use of compressed gas can be found in numerous applications from everyday items such as automobiles, jet engine propulsion, vacuum cleaners, air conditioners to large industrial scale compressors for chemical processing, transmission, and natural gas propulsion.
Apart from these, the gas compressor types are useful for a wide variety of applications, including : compressing intake air in gas turbines, transporting natural gas through pipelines, pressurizing aircraft cabins, providing compressed air for air brakes, storing purified gases in small volumes, storing air in submarines and moving heat in refrigeration systems.
In gas production operations, there are many cases in which the pressure of a gas must be raised to a higher value. When the pressure in a gas reservoir reduces, it will ultimately reach a point where it will no longer overcome all the pressure of the line into which the gas is being delivered and also pressure losses in the system. It then becomes essential to add a compressor to the system to increase the reservoir energy. And for this, we need to know the different types of gas compressors.
Types Of Gas Compressors
The compressors fall into two separate and distinct categories i.e. dynamic and positive displacement.
A) POSITIVE DISPLACEMENT
In a positive displacement compressor system, a certain inlet volume of gas is confined in a given space and subsequently compressed by reducing this confined volume or space. The gas, at this elevated pressure, is next expelled into the vessel system or discharge piping. Even though the positive displacement compressors include a wide spectrum of geometries and configurations, the most important process machines are helical screw rotating machines and piston compressors. The positive displacement machines operate on distinct portions of the fluid at a time and as such their operating speed, mechanical behavior is very different than dynamic machines. Examples of this type of compressors include reciprocating compressors, screw compressors, and scroll compressors.
Positive displacement is further divided into two sub-categories :
- Rotary
- Reciprocating
1) Rotary Compressor System
The rotary screw compressor is one type of positive displacement machine which has distinct working phases such as compression, suction, and discharge. One can find two counter-rotating helical screws arranged in a compressor casing, and the discharge nozzles, gas inlet are at the opposite ends. The rotary screw compressors are also suited to compress process gases. These compressor systems are further divided into - lobe, screw, liquid ring, scroll and vane compressor systems.
Lobe Compressor System - The rotary lobe compressor systems are used to provide air in pneumatic conveying lines for solids or powder.
Screw Compressor System - Usually used for continuous operation in industrial and commercial applications and may be either portable or stationary.
Liquid Ring Compressor System - Typically used as a vacuum pump, but can also be used as a gas compressor. The liquid-ring pumps are usually powered by an induction motor.
Scroll Compressor System - Also known as a scroll pump and scroll vacuum pump, the compressor system uses two interleaved spiral-like vanes to compress or pump fluids such as gases and liquids. One advantage with this, is they operate more quietly, smoothly and reliably than other types of compressors.
Vane Compressor System - The devices may be either a vacuum pump or a compressor with suitable port connections.
2) Reciprocating Compressor System
The reciprocating or piston compressor system uses the movement of a piston, driven by a crankshaft, within a cylinder to move gas from one pressure level to another higher pressure level. They can either be portable or stationary, can be multi or single staged, and can be driven either by internal combustion engines or electric motors. The automotive applications are driven by the small reciprocating compressors, while larger reciprocating compressors are still commonly found in large industrial applications. Moreover, multi-stage double-acting compressors are said to be the most efficient compressors available, in certain applications such as air compression. Just like the rotary, the reciprocating compressor system is divided into - diaphragm, double acting and single acting compressor systems.
Diaphragm Compressor System - Also known by the name membrane compressor, this is an alternative of the conventional reciprocating compressor. These are generally used for compressed natural gas and hydrogen, as well as in several other applications.
Double Acting Compressor System - The double-acting cylinder designs have two compressions, discharge areas, and a suction.
Single-Acting Compressor System - The single-acting cylinder designs have one compression, discharge area, and a suction.
B) DYNAMIC
Frequently called turbo compressors, these dynamic compressors are based on the principle of imparting velocity to a gas stream and converting this velocity energy into pressure energy. These compressors operate by continuously increasing the momentum of gas, as it flows through them and not relying on a trapped volume. Examples of compressors of this type include centrifugal/radial compressors, axial compressors, and mixed-flow compressors. The centrifugal machines perhaps comprise 80% or more of dynamic compressors, while the remaining 20% or less are axial flow machines, that are intended for low-pressure and higher-flow applications.
1) Centrifugal Compressor System
The centrifugal compressor system is primarily used for stationary, continuous service in industries such as chemical and petrochemical plants, oil refineries and natural gas processing plants. The compression is achieved by applying inertial forces to the gas using rotating impellers. In a centrifugal machine, the fluid flows into the machine parallel to the rotation axis and perpendicular or radially to the axis of rotation out of the machine. These, along with screw compressors, are extensively used in air conditioning systems and large refrigeration. These type of compressors are also used in internal combustion engines as turbochargers and superchargers. Apart from this, the centrifugal compressors are utilized in small gas turbine engines or medium-sized gas turbines (final compression stage). The centrifugal gas compressor types are generally suitable for high flow requirements.
2) Axial Compressor System
Large flow volumes in relatively small casings and with favorable power requirements can be handled by axial gas compressor types. The pressure range is low to medium for axial compressors. These industrial gas compressors are used where a compact design or high flow rate is required. The axial compressors can have high efficiencies. They are relatively expensive, as they require tight tolerances, high-quality materials and a large number of components. The axial compressors are used in medium to large gas turbines, some chemical plants, and natural gas pumping stations. In axial machines, the gas enters and exits the machine, parallel to the axis of rotation.
3) Mixed Flow Compressors
As its name suggests, the mixed flow machines are a mixture between purely centrifugal and purely axial machines. The only feature that makes it different from the other two dynamic compressors, is that it has a radial and axial velocity component at the exit from the rotor.
Comments
Post a Comment